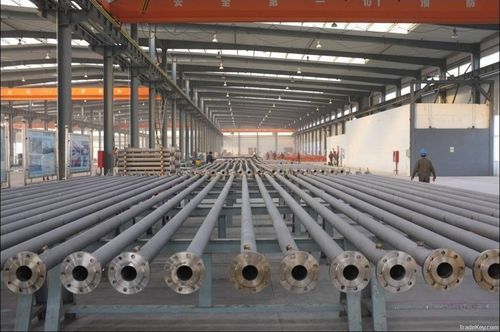
ریخته گری گریز از مرکز چیست؟
ریخته گری سانتریفیوژ یا گریز از مرکز (Centrifugal Casting) یک فرآیند تولیدی است که برای ایجاد اجزا و قطعات استوانهای با محور چرخش مرکزی استفاده میشود. این تکنیک شامل چرخاندن قالب حول یک محور مرکزی با سرعتهای معمولا بین ۳۰۰ تا ۳۰۰۰ دور در دقیقه در حین ریختن مواد مذاب در قالب است. ریخته گری گریز از مرکز یکی از روشهای نوین و کارآمد در صنعت ریختهگری است که با بهرهگیری از نیروی گریز از مرکز، تولید قطعات استوانهای با دقت بالا و خواص مکانیکی مطلوب را ممکن میسازد. این فرآیند شامل چرخش سریع قالب در حین ریختن مواد مذاب است که باعث میشود نیروی گریز از مرکز، مواد مذاب را به سمت دیوارههای داخلی قالب هدایت کند و محصولی متراکم و یکنواخت به دست آید. استفاده از این روش در تولید قطعاتی مانند لولهها و اجزای استوانهای توخالی، به دلیل مزایایی همچون کاهش تخلخل، توزیع یکنواخت مواد و دقت ابعادی بالا، بسیار مورد توجه قرار گرفته است.
شرکت آتی مهر با بهرهگیری از فناوریهای پیشرفته و دانش تخصصی در صنعت ریختهگری، به عنوان یکی از پیشگامان تولید لوله و اتصالات مقاوم به حرارت در منطقه شناخته میشود. این محصولات با طراحی دقیق و مواد اولیه باکیفیت، پاسخگوی نیازهای متنوع صنایع سنگین از جمله فولاد، نفت، گاز و پتروشیمی هستند. در این بخش، جزئیات کامل فرآیند تولید، کاربردها و مزایای این محصولات ارائه شده است.
- تولید لولههای ریختهگری به روش گریز از مرکز
- مواد اولیه: آلیاژهای خاص بر پایه آهن، کروم و نیکل که برای تحمل دماهای بالا طراحی شدهاند.
- کاربردها: این لولهها به طور خاص برای صنایع فولاد، نفت، گاز و پتروشیمی مناسب هستند، جایی که مقاومت در برابر خوردگی و فشارهای شدید ضروری است.
- مزایا: دوام بالا، مقاومت در برابر اکسیداسیون و طول عمر طولانی.
- تولید اتصالات مقاوم به حرارت به روش ریختهگری استاتیک
ریختهگری استاتیک برای تولید اتصالات مانند زانوییها، سهراهیها و فلنجها به کار میرود. در این روش، مذاب در قالبهای ثابت ریخته شده و با کنترل دقیق دما و زمان، استحکام و یکنواختی ساختار تضمین میشود.
- مواد اولیه: استفاده از آلیاژهای مقاوم به حرارت با ترکیبات خاص برای سازگاری با شرایط کاری سخت.
- کاربردها: مناسب برای سیستمهای انتقال مواد در دماهای بالا و محیطهای خورنده.
- مزایا: دقت ابعادی، مقاومت در برابر ترک و قابلیت استفاده در فشارهای بالا.
- تولید لوله و اتصالات مقاوم به حرارت صنایع نفت، گاز و پتروشیمی
لولههای زنگنزن آستنیتی مقاوم در برابر حرارت، به طور گستردهای برای ساخت لولههای کورههای ریفرمر و پیرولیز در صنایع پتروشیمی مورد استفاده قرار میگیرند. از این لولهها در پالایشگاهها نیز برای فرایند تبدیل گازها (مخلوطی از هیدروکربنها) و بخار آب به یک گاز غنی از هیدروژن و یا در کاربردهای دیگر مانند تولید آمونیاک و متانول استفاده میشود. این لولهها و سایر اجزای کورههای ریفرمر بایستی در مدت زمان طولانی تحت تأثیر درجه حرارت بالا، محیطهای تهاجمی و فشارهای داخلی نسبتاً زیاد در حالت بهرهبرداری قرار گیرند. شرایط معمول لولههای ریفرمر با دمای کاری در حدود 800 تا 1000 درجه سانتیگراد و فشار کاری 5 تا 40 کیلوگرم بر سانتیمتر مربع میباشد. بر اساس توصیه مؤسسه نفتی آمریکا، این لولهها عموماً برای عمر اسمی 100000 ساعت (4/11 سال) طراحی میشوند. با این حال، هنگامی که لولههای ریفرمر در معرض درجه حرارت بالا و فشار زیاد قرار گیرند، در اغلب آنها ترکخوردگی و خرابی زودرس به دلیل خزش و خستگی در طول عمر طبیعی لولهها اتفاق میافتد. عمر واقعی این لولهها از 30000 تا 180000 ساعت، بسته به کیفیت مواد و شرایط کاری، متغیر میباشد.
با توجه به لزوم استحکام خزشی و قابلیت ریختهگری گریز از مرکز، بالابودن میزان کربن در ترکیب این لوله¬ها ضروری است. با این حال، برخی از اشکال قطعات نظیر اتصالات Y و منحنیشکل توسط فرایند ریختهگری استاتیک نیز در قالبهای ماسهای تولید میشوند. مزیت اصلی روش گریز از مرکز در مقایسه با روش استاتیک، دستیابی به خلوص بالاتر در اثر نیروی گریز از مرکز ایجادشده در حین ریختهگری است که منجر به اثر شناوری شده و آلیاژ را از اکسیدها و ناخالصیها تصفیه میکند. به همین ترتیب، کنترل ساختار و ریزشدن دانهها باعث بهبود خواص مکانیکی و اکسیداسیون و همچنین افزایش قابلیت جوشکاری آلیاژ ریختهگری گریز از مرکز میشود. طی این فرایند، فلز مذاب تحت نرخ انجماد زیاد در قالب فلزی دوّار با سرعت زیاد (3000 – 300 دور در دقیقه) ریخته میشود. فلز مذاب بهصورت گریز از مرکز بهسمت دیواره داخلی قالب پرتاب شده و پس از سردشدن، جامد میشود. قطر داخلی دارای ناخالصی و اجزای اکسیدی بیشتری است که میتوان آن را ماشینکاری کرد.
- تولید لوله و اتصالات مقاوم به حرارت صنایع نفت، گاز و پتروشیمی
لولههای ساختهشده از فولادهای ریختگی مقاوم در برابر حرارت در تعداد زیادی از زمینههای صنعتی استفاده می شود، اما کاربرد اصلی آنها بهعنوان اجزاء اصلی در کورههای ریفرمر صنایع فولاد میباشد. این فرایند در کورههای ریفرمر انجام میشود، جایی که مخلوطی از هیدروکربن و جریان بخار از طریق صدها لوله عمودی عبور میکند. در اینجا، یک کاتالیزور پایه نیکل، واکنش گرماگیر را فعال میکند که عوامل واکنش را به هیدروژن مولکولی و منوکسیدکربن تبدیل میکند.
سینتیک این واکنش وابسته به پارامترهای فرایند، کاتالیزور و اندازه لولهها بوده و در محدوده دمایی 800 تا 950 درجه سانتیگراد و تحت فشار 5/3 تا 5 مگاپاسکال انجام میشود. کوره ریفرمر، محفظهای است که داخل آن از مواد نسوز پوشانیده شده و شامل چهار ردیف موازی است که هر ردیف حاوی 44 لوله تابشی آویزان عمودی است. ردیف مشعلهای گازی نصبشده در قسمت بالایی کوره، انرژی را برای واکنش گرمازا، گرمایش هیدروکربن و بخار از دمای ورودی (500 درجه سانتیگراد) تا دمای خروجی حاصل از محصولات واکنش (900 درجه سانتیگراد) تأمین میکنند. لازم به ذکر است که لولههای ریفرمر از سطح خارجی گرم میشوند. هر لوله از چند قطعه تشکیل میشود که توسط فرایندهای ریختهگری گریز از مرکز، ماشینکاری و جوشکاری قوس الکتریکی تنگستن گاز (GTAW) ساخته میشوند. مکانیزم اصلی آسیب که عمر این لولهها را محدود میکند تغییر شکل خزشی است که توسط فشار داخلی ایجادشده در شرایط کاری عادی و تنشهای گرمایی ایجادشده در طی سیکل¬های راهاندازی و خاموششدن کوره ایجاد میشوند.
ترکیب شیمیایی این لولههای خاص برای چندین دهه مورد بررسی قرار گرفته و پیشرفتهای گستردهای نیز در زمینه بهبود استحکام مکانیکی در دمای بالا حاصل شدهاست.
از مزیتهای ناشی از افزایش استحکام خزشی لولههای ریفرمر میتوان به موارد زیر اشاره کرد:
- افزایش طول عمر لولهها، فواصل زمانی بیشتر بین تعمیرات و کاهش توقفات خارج از برنامه تولید.
- کاهش ضخامت دیواره لوله و در نتیجه افزایش انتقال حرارت و یا بازده بهتر فرایند (افزایش حجم کاتالیزور به دلیل قطر داخلی زیادتر لوله) و همچنین مقاومت بهتر در برابر خستگی حرارتی بهعلت کاهش شیب دمایی در سطح مقطع عرضی لوله.
همه عوامل فوق باعث کاهش هزینههای فرایند میشوند.
- ویژگیها و استانداردهای کیفی
- مقاومت حرارتی: توانایی تحمل دماهای بیش از 1000 درجه سانتیگراد بدون از دست دادن خواص مکانیکی.
- ضد خوردگی: پوششدهی و آلیاژهای ویژه برای محافظت در برابر اسیدها و مواد شیمیایی.
- تطابق با استانداردها: تولید مطابق با استانداردهای بینالمللی نظیر ASTM و ISO.
- کاربردها
این محصولات در پروژههای زیرساخت، پالایشگاهها، نیروگاهها و واحدهای تولیدی فولاد به کار میروند. از جمله موارد خاص میتوان به خطوط انتقال گاز طبیعی، سیستمهای خنککننده و تجهیزات فرآوری مواد معدنی اشاره کرد.
- چرا ما را انتخاب می کنید؟
- تجربه بیش از یک دهه در صنعت ریختهگری.
- تیم مهندسی متخصص برای طراحی سفارشی.
- تعهد به تحویل به موقع و خدمات پس از فروش جامع.